SmartEM – Open reference architecture for engineering model spaces
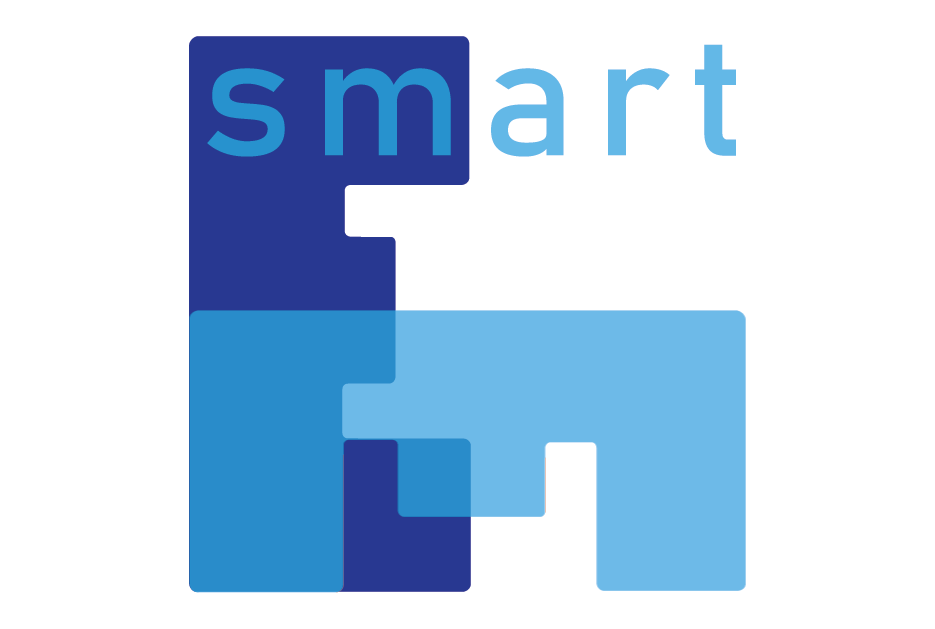
Today, engineers use "computational engineering models" in the design and development process. These models make it possible to simulate and adapt essential properties of the objects being developed in the computer. However, the ability to combine existing individual models into a complete system has been limited. Such digital twins often have to be created manually - a time-consuming process with many functional limitations.
The SmartEM project is developing a standardized system for creating, sharing, and reusing computational engineering models. The work is driven by a multinational consortium of partners from academia, data science and industry. The consortium is developing a flexible reference architecture that can be used to combine and align engineering models from different sources. The architecture is based on open data space concepts such as Gaia-X. In addition, AI-based methods will be used to generate simplified versions of complex models, called surrogate models, from heterogeneous data sources. These simplify the exchange and integration of models. This is expected to lead to new approaches in product design and development.
The reference architecture classifies design models into a taxonomy, which improves their interoperability and reusability. At the same time, the project consortium is developing an IP management system that creates the legal basis for the use and exchange of models. SmartEM increases efficiency in the engineering sector by providing a robust and flexible modeling environment. These approaches foster collaboration between different stakeholders and accelerate the digital transformation of engineering. Another goal of the project is to reduce development costs by reusing, recombining or training existing hybrid and data-based models.
The developments planned in the SmartEM project promise a wide range of applications in several industries. In the field of Additive Manufacturing (3D printing), the evaluation of production data enables more precise and qualitatively improved production at lower costs and with less waste. In the development of wind turbines and hydrogen engines, linking flow and structural models can lead to more efficient designs and shorter development cycles. Another application is process optimization in gear grinding. Here, AI algorithms continuously analyze and adjust production parameters to increase efficiency, minimize downtime, and improve quality.
The project is funded by the European Eureka cluster ITEA4.
Project partners
- Katholieke Universiteit Leuven, Belgium
- Siemens Industry Software NV, Belgium
- Canon Production Printing Netherlands B.V., The Netherlands
- Eindhoven University of Technology, The Netherlands
- Philips Consumer Lifestyle B.V., The Netherlands
- Reden BV, The Netherlands
- SemLab, The Netherlands
- Thermo Fisher Scientific, The Netherlands
- TNO, The Netherlands
- Acd Bilgi Islem ltd.sti., Türkiye
- Alpata Technology, Türkiye
- Inovasyon Muhendislik, Türkiye
- Fraunhofer SCAI, Germany
Project duration: 04/2024 until 03/2027